В промышленном производстве, особенно в высокотехнологичных наукоемких отраслях, таких как авиакосмическое машиностроение, радиоэлектроника, автомобилестроение, наряду с традиционными технологиями, все больше находят применение ультрасовременные способы формирования деталей.
Так, одним из наиболее эффективных методов получения высококачественных изделий из металлов и сплавов является выращивание заготовок и деталей. В зарубежной практике такая технология носит названия: Selective Laser Sintering, Direct Metal Fabrication, Direct Manufacturing. Принцип формирования изделий при такой технологии заключается в послойном выращивании изделия, путем сваривания или спекания порошкового материала. В итоге можно получать детали сложной формы, которые обычными методами литья изготовить просто невозможно.
При такой технологии деталь создаётся добавлением новых слоёв к уже существующим и этим кардинально отличается от традиционных способов обработки заготовок резанием, когда из заготовки, "отсекая лишнее", получают готовую деталь. Новые методы способствует уменьшению расхода материалов и повышению производительности, что очень важно при создании опытно-промышленных образцов и готовых деталей.
Различают две группы методов, используемых для выращивания металлических деталей, которые отличаются способом соединения порошковых частиц в единое целое. Они соответственно основаны на лазерном спекании и осаждении порошков.
К первой группе методов относится технология спекания, которая была разработана в 1992 году фирмой DTM (в настоящее время это департамент 3D Systems Inc.). В этом случае тепло лазера соединяет вместе связующий полимер и металлический порошок, после чего изделие помещается в печь, где удаляется связующее, происходит инфильтрация и спекание металлического порошка.
Обработка лазером заключается в следующем. Вначале с помощью CAD-системы производится компьютерное проектирование процесса, включающее создание чертежа детали и разработку технологии нанесения покрытия. Затем в специальной камере с помощью ролика на подложку наносится слой металлического порошка и полимера. Толщина слоя выбирается из соображений прочности конкретно для каждой детали.
Лазерный луч, управляемый компьютером, «пробегает» по поверхности и спекает металл и полимер именно в тех местах, где необходимо, создавая при этом первый слой детали. Далее валик наносит новый слой порошка, после чего цикл повторяется до тех пор, пока не произойдет спекание всех частей будущего изделия.
Вот характеристики готового изделия, полученного на оборудовании Vanguard™ HS SLS system с помощью порошка LaserForm A6:
Удельный вес: 7,8 кг/м3
Предел текучести: 470 MПa
Предел прочности на разрыв: 610 MПa
Относительное удлинение: 2.0 - 4.0%
Модуль Юнга: 138 ГПa
Твердость
- после инфильтрации: HRС = 10 – 20 (полированная поверхность);
- после спекания: HRС = 39
Теплопроводность: 39 Вт/(м·°С)
Различные порошки, используемые в качестве сырья, позволяют получать цельнометаллические изделия из драгоценных металлов, инструментальных, конструкционных сталей, кобальт-хромовых и других сплавов.
Наряду с лазерными технологиями, существуют методы осаждения порошков на поверхность с помощью специальных технологических решений. Технология Ultrasonic Consolidation основана на использовании вместо лазера ультразвука, который спекает слои порошка друг с другом.
Технология Electron Beam Melting заключается в послойном построении детали из металлического порошка, расплавляемого электронным пучком. Так называемая электронно-лучевая плавка обеспечивает мощный нагрев и высокую производительность установки. Процесс формирования детали происходит в вакууме при высоких температурах, что, вследствие уменьшения остаточных напряжений, способствует получению механических свойств, превышающих аналогичные свойства для литых и кованых деталей.
Существуют и другие методы, относящиеся к аддитивному производству, некоторые из них поставлены на поток и успешно работают в промышенности. Другие – находятся в состоянии разработки или используются в научных целях. В любом случае, принцип действия нового класса оборудования позволяет полностью решать проблему ликвации примесей и химической неоднородности, которая присутствует в литых изделиях, при сохранении комплекса механических свойств на уровне литых изделий и деталей, обработанных давлением. Аддитивными методами производства можно получать цельнометаллические детали, полые внутри или имеющие различные перегородки, что невозможно в практике обычного литейного производства. Также возможно получать изделия не только из металлов, но и из полимеров, керамики, композиционных материалов, в том числе и для изготовления литейной оснастки – форм, стержней и моделей. Указанные выше методы полностью компьютеризированы, и весь процесс проектирования и производства происходит с помощью специализированного программного обеспечения. Так, сотрудниками нашей компании разработаны основные технологические этапы создания моделей из полимерных материалов и общие решения по методам литья по выплавляемым и выжигаемым моделям.
Выращивание детали электронным пучком
Выращивание металлического слоя детали электронным пучком - способ Electron Beam Melting
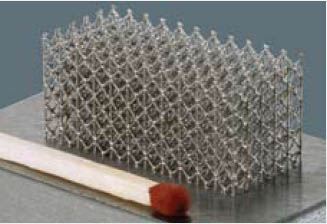
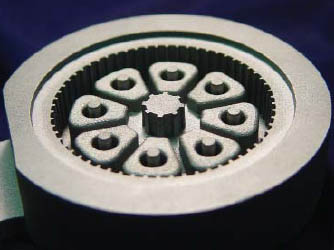