Надежность и долговечность многих конструктивных элементов и технологических машин во многом зависит от эксплуатационных характеристик узлов трения. Подшипники скольжения, подпятники, уплотнения и прочие подобные узлы в настоящее изготавливаются из различных материалов, которые отличаются по своим механическим и физико-химическим характеристикам, стоимости и выбираются, исходя из условий эксплуатации. Наряду с традиционными материалами, которые уже завоевали свою нишу в изготовлении подшипников скольжения (баббиты, бронзы, цинково-алюминиевые сплавы, чугун, сталь, алмаз, иногда кадмий или серебро и др.), ведущие мировые и отечественные производители подшипников используют разнообразные композиционные и порошковые материалы. Самосмазывающиеся материалы позволяют отказаться от дорогостоящей системы маслоподачи и особенно востребованы там, где подача смазки затруднена или противопоказана (например, в пищевой промышленности). Подшипники скольжения из таких материалов также выгодно использовать в агрессивных коррозионных средах или при температурах, превышающих рабочие для существующих видов смазок.
Очевидно, что для той же пищевой промышленности вполне применимы композиционные материалы, состоящие из несущей основы из стекловолокна, пропитанного эпоксидной смолой. Такая армирующая основа содержит смазывающие элементы, изготовленные из тефлона или полиэстера.
Одним из материалов подобного класса является Duralon. По заявлениям производителя подшипники из такого композита выдерживают до 25 миллионов циклов при нагрузке 4000 фунтов (27,58 МПа) на квадратный дюйм или 1 млн. циклов при нагрузке 20000 фунтов на квадратный дюйм (137,0 МПа). Duralon применяется в пневмоцилиндрах промышленных установок, лебедках и шкивах, работающих на морских судах при погрузке-выгрузке, ленточных конвейерах и т.д. Рабочие температуры изделий изменяются от криогенных до 160 °С.
Подобные же материалы предлагаются и другими производителями и могут отличаться в том числе и конструктивными особенностями. Например, тефлон (политетрафторэтилен) – это довольно мягкий, пластичный материал, который армируется не только тканями с эпосксидной смолой, но и металлическими или керамическими порошками. Это значительно увеличивает его прочность, чему также способствует использование подложки из нержавеющих сталей или бронз.
Наряду с ПТФЭ, для создания смазочного слоя в самосмазывающихся подшипниках широко используется графит. Естественно, физико-механические свойства графита не позволяют использовать его в виде монолитных деталей, поэтому в большинстве случаев чешуйки этого материала связаны термоусадочными смолами или карбоном. Также существует класс материалов, которые представляют собой металлы, пропитанные графитом. Использование металлов в качестве несущей основы связано не только с повышением механических свойств изделия, но также и с температурной составляющей. Именно такие материалы (Dryslide, Graphalloy) позволяют эффективно отводить тепло от узла трения.
Одним из подобных материалов является Graphalloy, который может иметь различные основы: баббиты, серебро, бронзы, медь и железо. При этом диапазон рабочих нагрузок колеблется от 5000 до 6000 фунтов на квадратный дюйм (34-41 МПа), а максимальные нагрузки достигают 130-170 МПа.
Также перспективным классом самосмазывающих материалов для подшипников скольжения является дисульфид молибдена, который может быть связан металлами или эпоксидной смолой. Довольно часто кристаллы Mo2S используется в подшипниках из пластика. В таком случае несущей основой подшипника может являться нейлон, ацеталь или полиамид. В работе подшипников из указанных материалов весьма важным является охлаждение узла трения, которое можно производить окунанием в воду или другую жидкость или газ (аммиак, пропан и др.). Такое охлаждение способствует возникновению в узле трения гидродинамической пленки, которая снижает ударные нагрузки и уменьшает негативное действие переходных процессов, возникающих при выходе на рабочие скорости вращения. Поэтому подшипники на основе дисульфида молибдена довольно часто дополнительно смазываются специальными синтетическими маслами, что существенно увеличивает срок службы узла, приближая его к характеристикам металлических подшипников.
Помимо самосмазывающихся композитных подшипников, широкое распространение получили подшипники скольжения, созданные методами порошковой металлургии. Наличие в структуре таких изделий пористости позволяет предварительно пропитывать подшипники различными смазками. Во время работы подшипника, удерживаемое в порах масло под воздействием температуры начинает выделяться наружу и образует смазывающую плетку в узле трения. После остановки механизма масло впитывается обратно в поры и удерживается внутри до следующего рабочего цикла. Способы спекания позволяют варьировать величину пористости до 35%, что способствует сохранению эффекта самосмазываемости в течение 3000-5000 ч. Износостойкость подшипников скольжения, изготовленных методами порошковой металлургии, в несколько раз выше, нежели у традиционных металлических изделий.
В отечественной и зарубежной практике для получения подшипников скольжения используют, главным образом, бронзы и стали с добавками графита, цинка, серы и других компонентов, уменьшающих коэффициент трения. Пропитка пор может осуществляться металлами, пластмассами и различными маслами. Состав и пористость изделия зависит от назначения и условий работы подшипника или втулки и выбирается нашими конструкторами на основе тщательного анализа указанных факторов. При этом материал и способ пропитки также зависит от конкретного заказа. На основании проведенного анализа выбирается способ спекания и дальнейшей обработки, включающей возможность повторной пропитки.
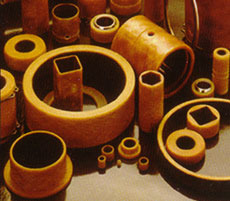
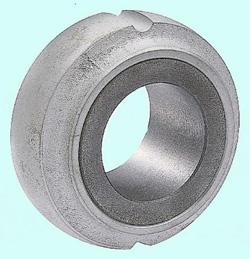
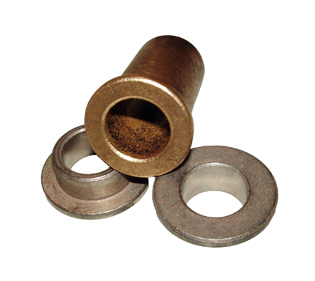